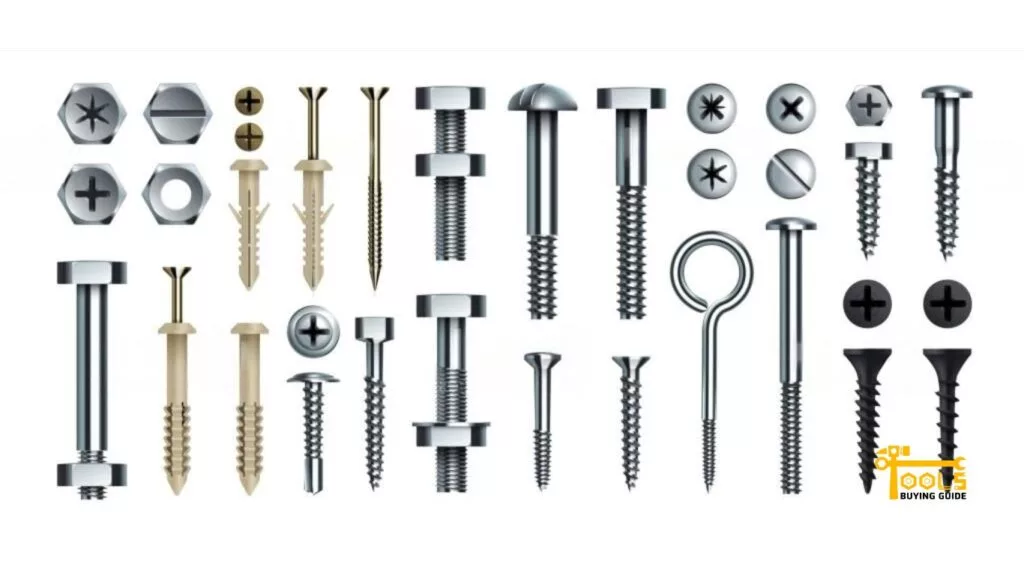
Rivets have been around since antiquity and are still an integral part of many industries today. They join two materials, typically metal or plastic, securely with a sturdy bond. Different types of rivets are used for different applications. From automotive to appliance manufacturing, rivets play a vital role in keeping parts and structures together.
The type of material being joined together requires a certain type of rivet. For example, aluminum needs a blind rivet, while steel needs more powerful solid rivets or button-head rivets for metal.
Let’s explore the seven common rivet type and the materials used to make them. So, whether you’re a manufacturing professional or not, it’s worth learning about the different types of rivets that are available.
What are the Different Types of Rivets?
There are seven common types of rivets, each with its own benefits and what are rivets used for.
Blind rivets
Blind rivets are tubular in shape and feature a mandrel through the center. This mandrel causes the rivet to expand when pulled through a hole in the materials being joined together. This provides an incredibly strong bond.
Blind rivets are commonly used with materials that require an incredibly secure bond or for applications with limited access to one side of the material. This makes them extremely popular in a variety of industries.
Solid shank rivets
Solid shank rivets are similar to blind rivets but don’t have a mandrel through the center. The solid shank rivet is a one-piece fastener, and the head of the rivet does not move. You must use a special tool to drive the rivet through the material, usually at a lower pressure than blind rivets.
Solid shank rivets provide a stronger bond than blind rivets and generally come in larger sizes. They are best suited for applications that require additional strength or resistance to vibration since the head of the rivet does not move.
Tubular rivets
Tubular rivets are similar to solid shank rivets in shape and size but have a hollow center. This allows them to be driven from one side of the material and then expand on the other. The head of the rivet does not move during this process.
Tubular rivets provide slightly less strength than solid shank rivets, but they are still a reliable option for creating a secure bond. They are commonly used in applications that require additional vibration resistance or when access to one side of the material is limited.
Split rivets
Split rivets are similar to solid shank rivets but have a split on one end. This allows them to be driven into materials from one side and then expand on the other. The head of the rivet does not move.
To install split rivets, you must use a special tool to drive the rivet through the material. It’s important to ensure that the joined materials are of similar thickness to create an even and secure bond. The vibration resistance of this type of rivet uses slightly less than that of solid shank and tubular rivets.
Sealed/C sealed rivets
Sealed or “C”-sealed rivets feature an internal sealant to provide additional vibration resistance. They are often used in applications where the joined materials may be exposed to extreme temperatures or harsh conditions.
The sealant helps to protect the bond by preventing water and other particles from entering. These rivets come in various shapes, sizes, and materials, depending on the application. They are typically more expensive than solid shank or blind rivets, but they provide added protection for your projects.
Read More About the Angle Grinder Blade
Shoulder/huck bolts
Shoulder or huck bolts feature a large head on one end that fits into a hole in the material being joined together. The other end features a threaded shank for attaching nuts and washers. This type of rivet can create an incredibly strong bond between two materials.
The shoulder of the bolt provides additional vibration resistance and helps to create a secure fit. Shoulder or huck bolts are commonly used in aerospace applications and for joining materials of different thicknesses.
Peel-type blind rivet nuts
Peel-type blind rivet nuts are used for attaching threaded fasteners to thin materials. The rivet nut is inserted from one side, while a special tool is used to expand the rivet on the other side. This creates a secure bond that can withstand heavier loads than traditional blind rivets.
The applications where peel-type blind rivet nuts may be used are limited, but they are commonly used in heavy-duty projects where a secure bond is required. These rivets have become more popular due to their strength and ease of use.
Materials Used for Rivet
Rivets are constructed from various materials, each designed to meet the specific needs and demands of different applications.
Aluminum rivets
Aluminum rivets are lightweight, corrosion-resistant, and relatively soft, making them easy to install. These sheet metal rivets are frequently used in the construction, automotive, and aerospace industries.
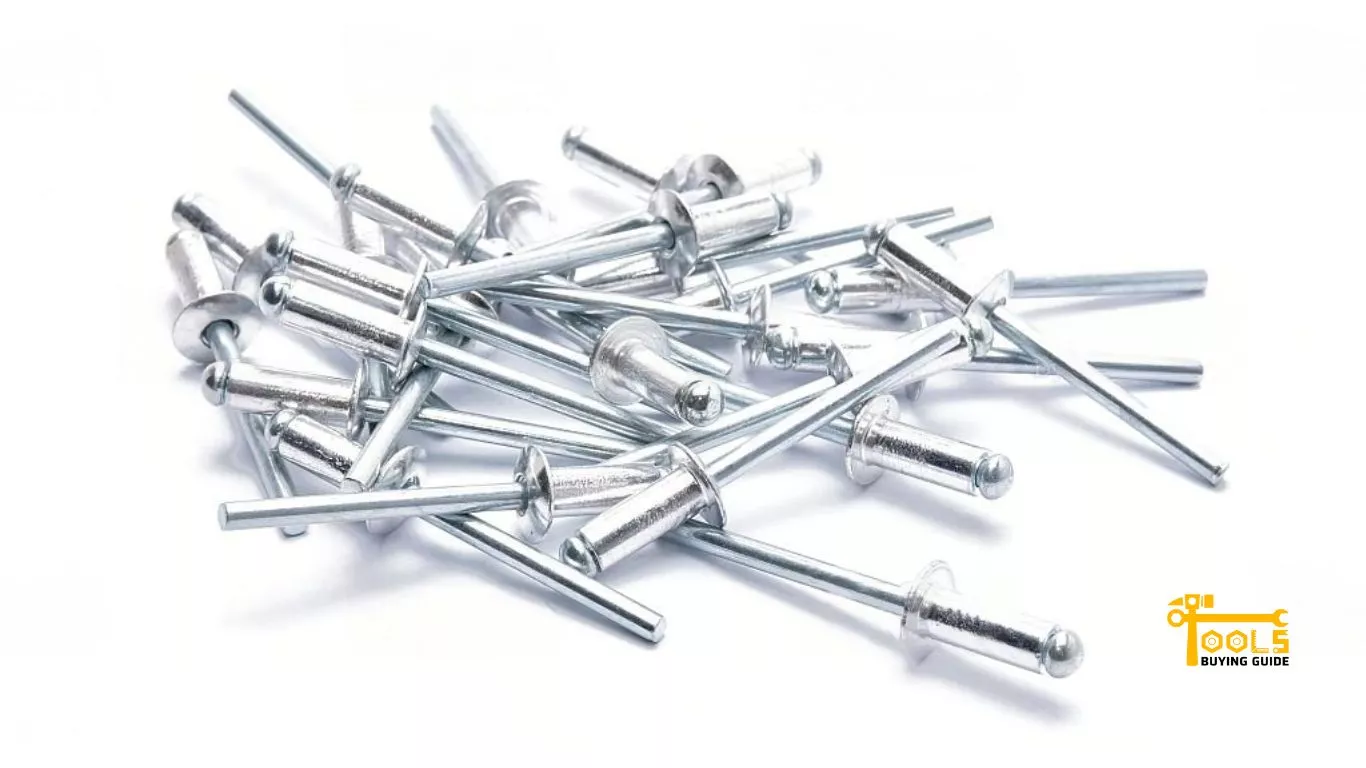
Steel rivets
Known for their exceptional strength and durability, steel rivets are used in applications that require resistance to high stress and heavy loads. They are widely used in the shipbuilding, bridges, and structural steel industries.
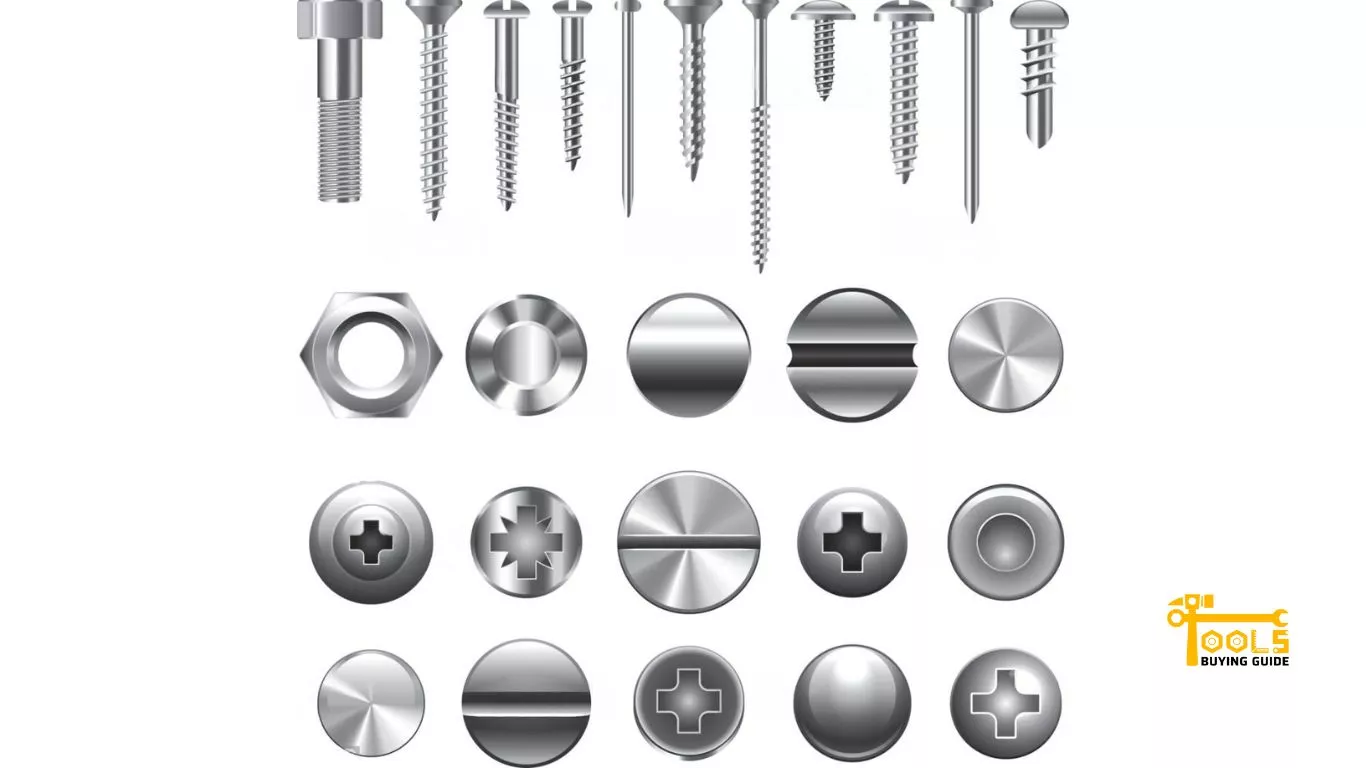
Stainless steel rivets
These rivets combine the strength of steel with superior corrosion resistance. They are ideal for outdoor applications or those exposed to corrosive environments, such as marine or food processing industries.
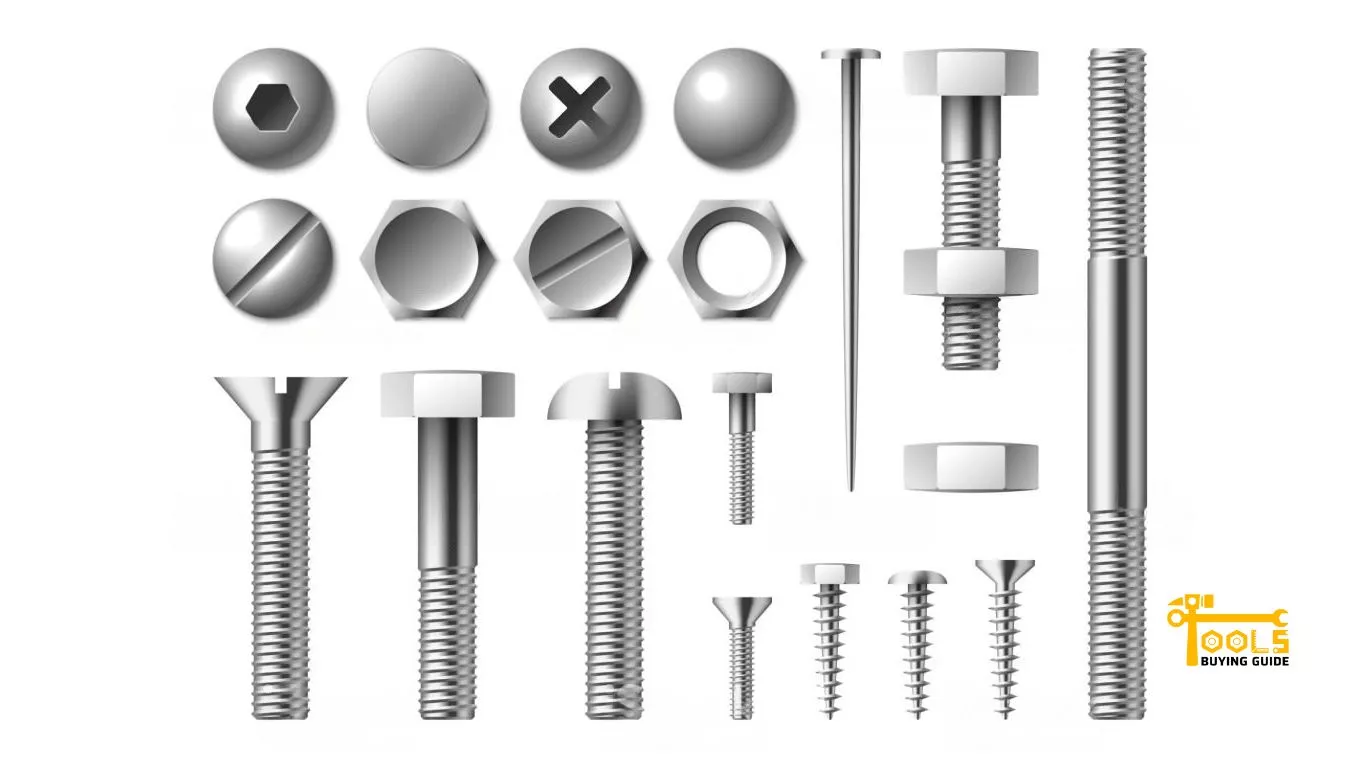
Copper rivets
Copper rivets are known for their excellent electrical conductivity and corrosion resistance. These properties make them ideal for the electrical and electronics industries.
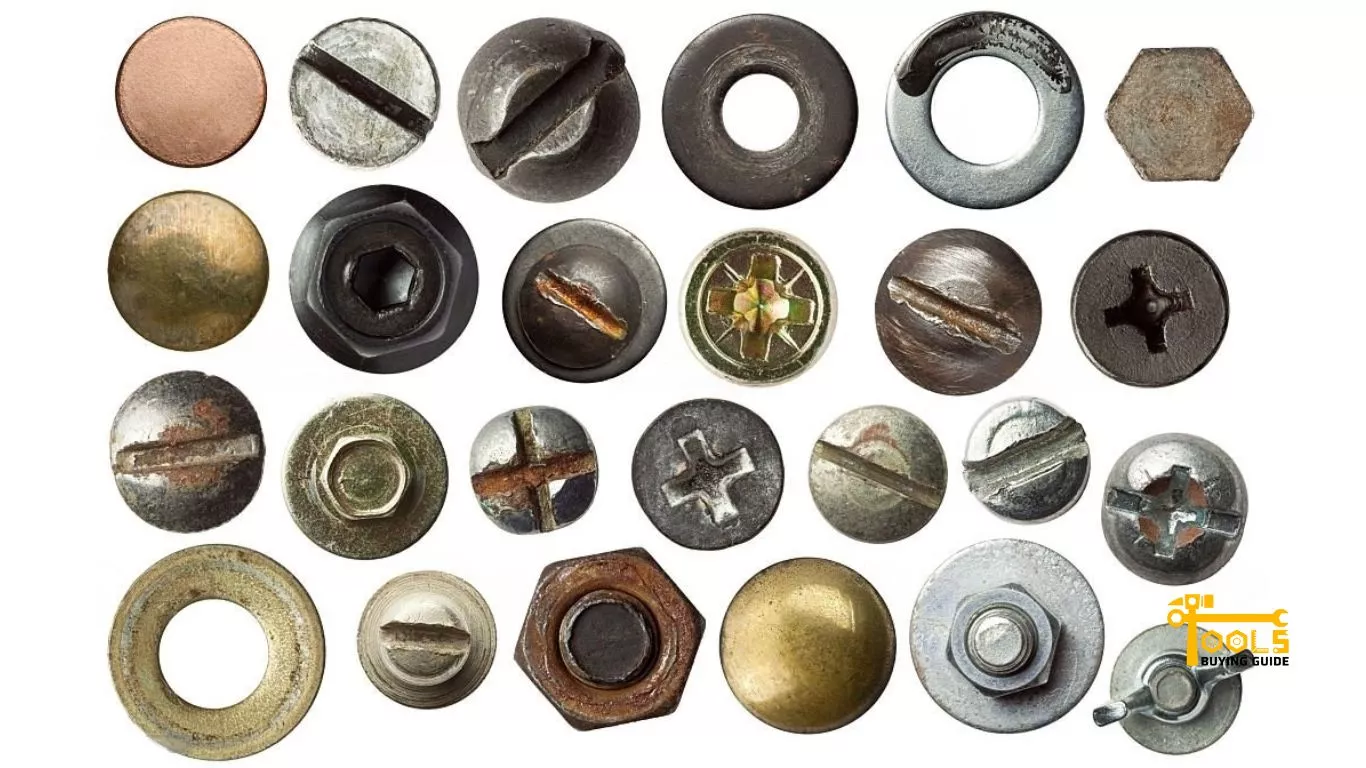
Monel rivets
Monel, a nickel-copper alloy, is used for rivets that withstand extreme temperatures, corrosion, and harsh chemical environments. These rivets are often employed in the oil and gas industry, chemical processing, and marine applications.
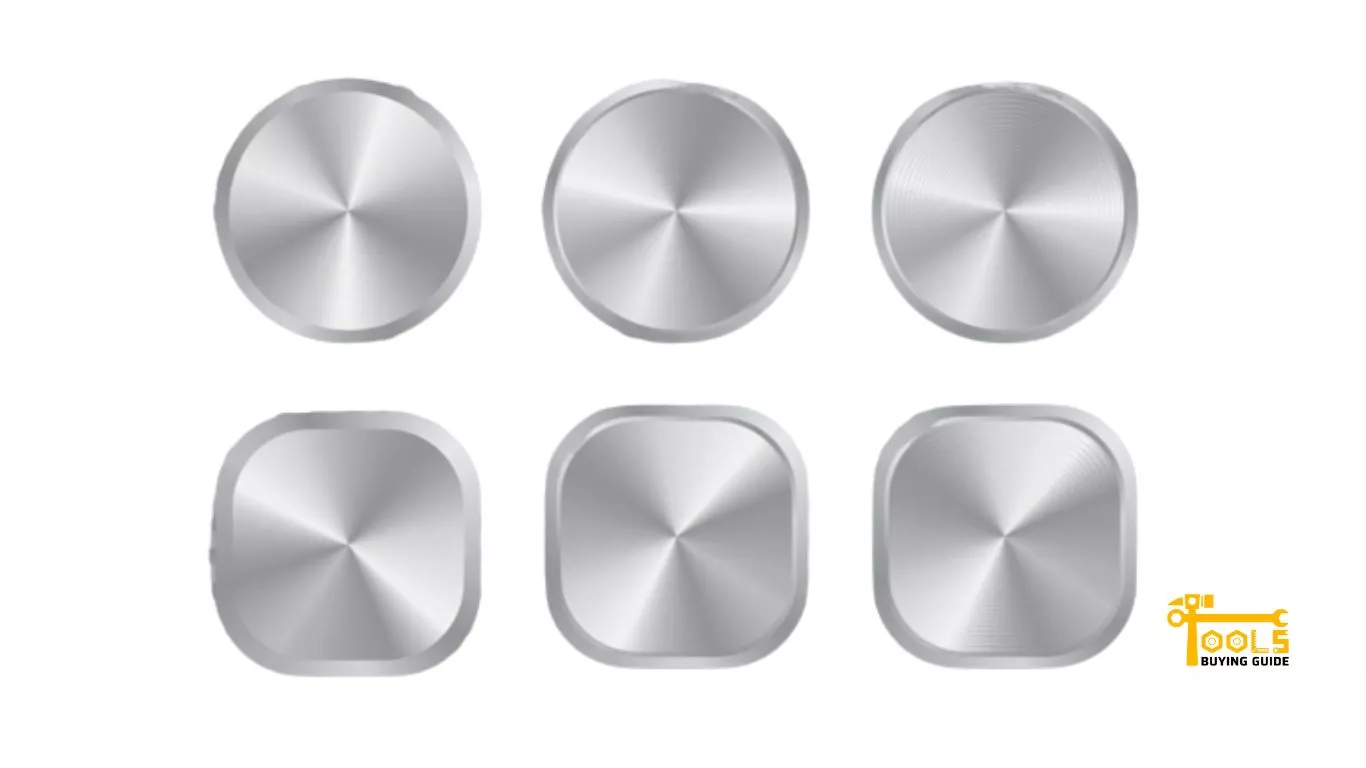
Plastic rivets
Plastic rivets are lightweight, corrosion-resistant, and electrically insulating. They are commonly used in electronics, automotive interiors, and consumer goods.
Each material has unique properties that determine its suitability for a particular application. Therefore, it’s essential to choose the right rivet material for your specific purpose to ensure a secure and durable connection.
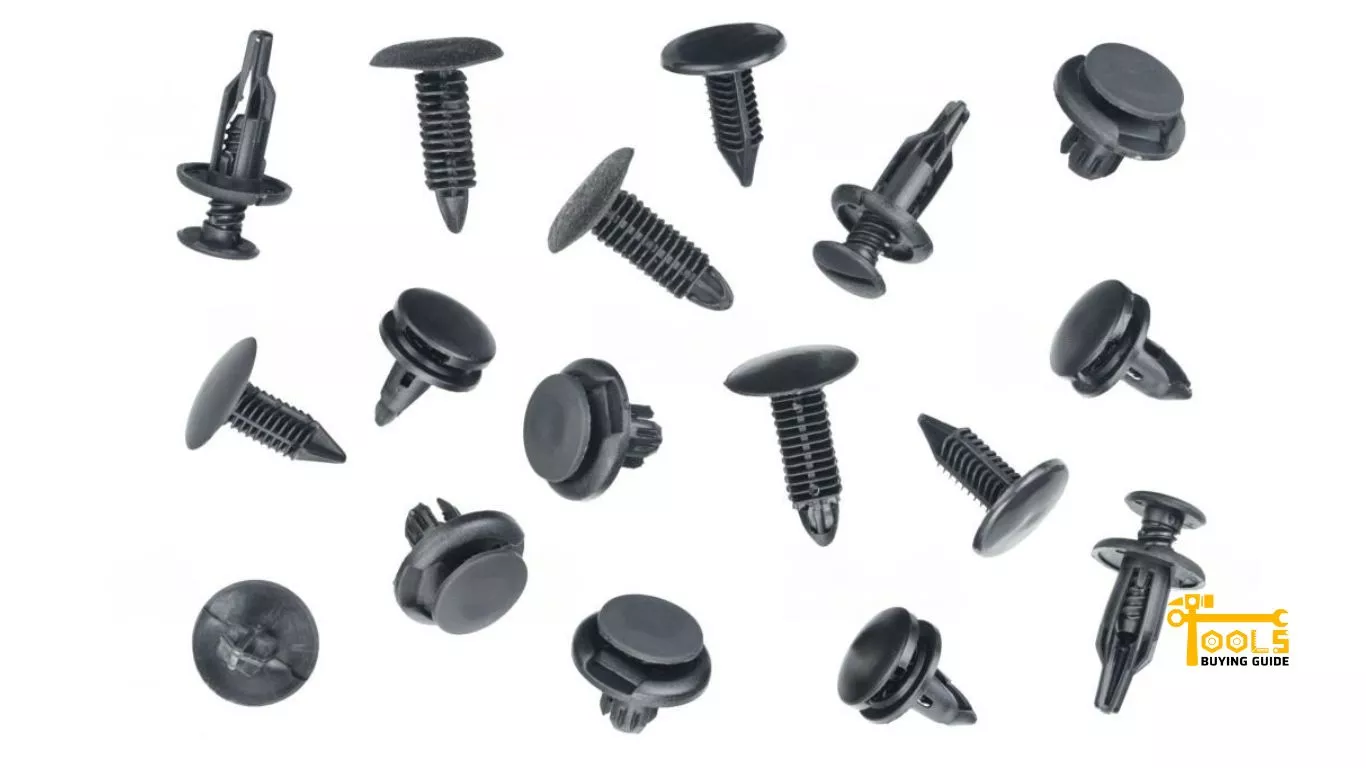
How Do Rivets Work?
Rivets create a mechanical and/or chemical bond between two pieces of material. When the rivet is inserted into a hole in one piece of material, its head expands to create a secure connection. The rivet bonds with the second piece of material when driven through the hole.
The expansion of the rivet’s head creates a high degree of surface contact between the two pieces of material, increasing the bond’s strength and stability. This is why riveting is often used in applications that need to resist high levels of vibration or tension.
When using solid shank rivets, it’s important to ensure that the joined materials are similar in thickness for an even and secure bond. Tubular and split rivets are better suited for joining materials of different thicknesses, as they can expand on one end while remaining secure on the other.
Applications of Rivets
Rivets are used in many industries for a variety of purposes. Some common applications include:
Automotive industry
Rivets have been used in the automotive industry for decades. They secure body panels, dashboards, interior trim, and bumpers. They can also be used to fasten electrical components or other hardware. The strength of riveted bonds makes them ideal for use in high-stress areas such as engine compartments and wheel wells.
Sealed rivets can provide extra protection against moisture and other contaminants for parts that are exposed to the elements. Shoulder or huck bolts may also be used in automotive applications requiring additional strength.
Aerospace industry
Rivets are essential for aerospace engineering, as they provide strength and durability in aircraft design. Rivets are used to construct airframes, fuselages, wings, and other components of an aircraft. They help create a secure bond between materials that can withstand extreme temperatures and pressures during flight. Additionally, riveting is often used to reduce the overall weight of an aircraft, allowing for maximum performance and fuel efficiency.
Sports equipment
Rivets are used to manufacture sports equipment such as bicycles, golf clubs, skis, and snowboards. Their strong bond is essential for ensuring these items remain intact during vigorous use.
For instance, most bicycle frames are held together with rivets. The head of the rivet provides a secure connection and prevents the frame from coming apart when subjected to heavy loads or vibrations.
In addition, many golf clubs feature riveted joints for added strength and stability. Rivets are also used in ski poles and snowboard bindings to ensure these items remain secure during use.
Frequently Asked Questions
Steel is the most common material for making rivets due to its durability, strength, and cost-effectiveness. Other rivet materials include aluminum, brass, copper, stainless steel, and many non-metallic materials, such as plastic.
The choice of material for riveted joints largely depends on the materials being joined together. Typically steel, aluminum, copper, and brass are commonly used.
Steel rivets are most suitable for riveting steel due to their hardness and strength, which match the qualities of the steel being joined. Steel rivets are also corrosion-resistant, which is beneficial for outdoor use.
Rivet materials can usually be identified by a specific color or a stamped logo on the head of the rivet. Steel rivets typically have a gray finish, while aluminum will have a lighter color finish. Brass and copper have a yellowish-brown finish, while stainless steel will have a slightly shinier silver color.
Solid rivets, often made from steel, are the strongest. The second strongest type is shoulder or huck bolts, which feature a large head on one end and a threaded shank on the other. These rivets provide additional vibration resistance and can be used to join materials of different thicknesses.
Plastic rivets are much lighter than metal ones and offer good corrosion resistance and electrical insulation. However, they are not as strong as metal rivets and may not withstand heavy loads or extreme temperatures.
Conclusion
Rivets are an incredibly useful fastening solution for various materials and projects. With modern advances in manufacturing, many types of rivets and materials are used for rivet production.
Whether you’re working with aluminum, stainless steel, or other materials, there is sure to be the perfect rivet available. From durable and resilient steel rivets to lightweight aluminum rivets, there is sure to be an option that fits the needs.
Be sure to research the best type and material for your project before purchasing any supplies to get the right product.
[…] Read Also: Different Types of rivets […]